OBC in EVs: Functional Overview
This article focuses solely on unidirectional OBCs and does not cover bi-directional OBCs.
Read an interesting article of History of EV Charging to gain more details on evolution of EV charging.
This article delves into the fundamental aspects of the On-Board Charger (OBC) in Electric Vehicles (EVs). It covers the purpose of the OBC, its various interfaces (AC, DC, thermal, low voltage, and safety), and the major components involved in its operation, such as power converters, filters, and controllers. Additionally, the article explains the critical functions the OBC performs, including energy conversion, communication with the EV’s systems, and ensuring safe and efficient battery charging. By the end, readers will gain a comprehensive understanding of how the OBC enables seamless charging experiences while ensuring adaptability, safety, and reliability in EV systems.
OBC in EVs:
The OBC in an EV is a fundamental system that bridges the gap between external power sources and the EV’s battery. Its primary purpose is to convert AC power from the grid into DC power suitable for battery charging. The OBC is crucial for EVs as it provides flexibility to charge batteries directly from common electrical outlets, eliminating the need for specialized external equipment like DC fast chargers in most day-to-day scenarios.
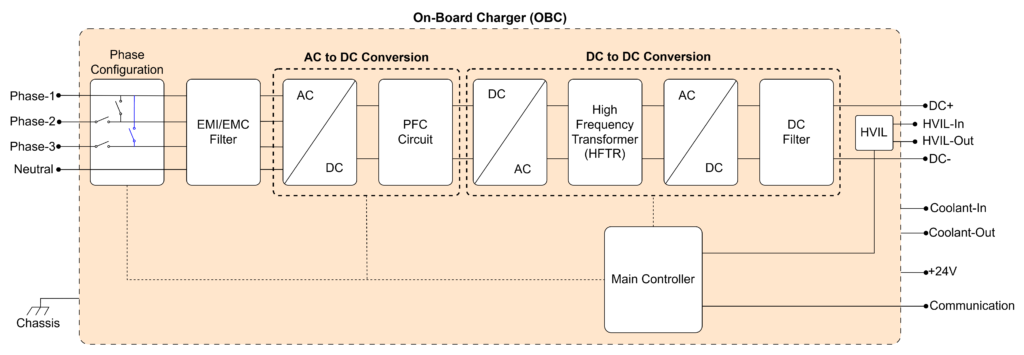
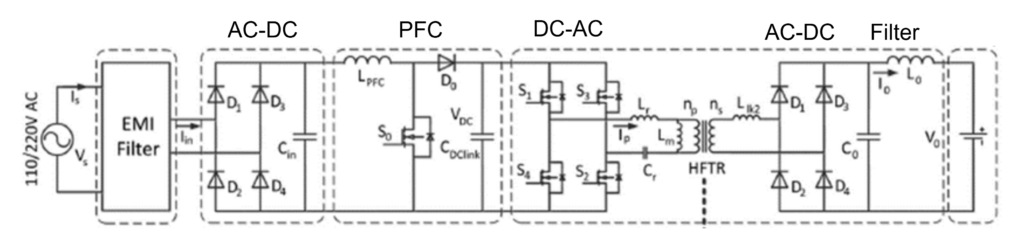
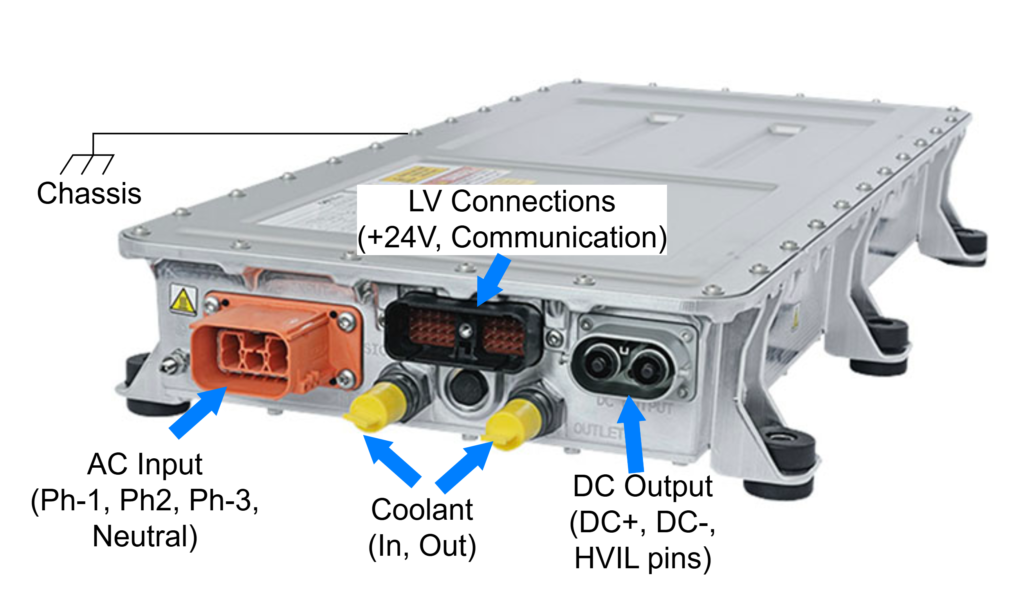
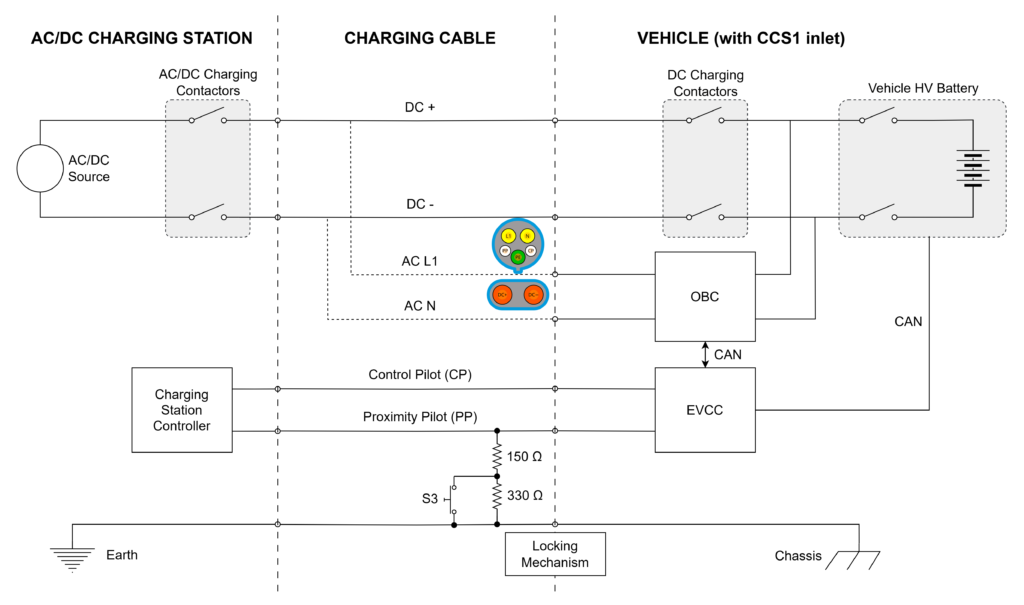
Let’s look into the differences interfaces of OBC:
Interfaces:
The OBC interfaces with various systems in the vehicle and external environments. These interfaces include:
- AC Input:
- Phase1, Phase2, Phase3, Neutral: The OBC can connect to single-phase or three-phase AC supplies depending on the grid configuration and power requirements. This flexibility allows it to operate in different regions with varying electrical standards.
- DC Output:
- DC+ and DC-: The OBC provides high-voltage DC output for charging the battery.
- HVIL Pins: High Voltage Interlock Loop (HVIL) ensures safety by monitoring the integrity of high-voltage connections (here, DC output connection). Read more details about HVIL at HVIL Explained
- Thermal Interfaces:
- Coolant-In and Coolant-Out: These interfaces manage the thermal regulation of the OBC. Liquid cooling is typically used to maintain the operating temperature within safe limits even during high power loads.
- Low Voltage Interfaces:
- 24V Supply: Powers the control and auxiliary systems within the OBC, such as sensors and the main controller.
- Communication Interface (e.g., CAN): Enables data exchange with the Electric Vehicle Communication Controller (EVCC) for monitoring and control. This interface is critical for synchronizing charging operations with the vehicle’s overall system.
- Hardware Interfaces (e.g., Charging Enable) (Optional): Provides additional safety and control mechanisms, ensuring that charging only begins under proper conditions. (Note: These interfaces are NOT shown in the picture).
- Safety:
- Ground Connection: The metallic body of the OBC is grounded to prevent electrical hazards and ensure compliance with safety regulations. Proper grounding protects both the user and the vehicle from potential electrical faults.
Major Components and Their Functions:
The OBC comprises several critical components that work together to achieve efficient and safe battery charging:
- Phase Configuration:
- The OBC supports both single-phase and three-phase configurations. It can function as a three-phase OBC by connecting to three different phases or as a single-phase OBC by using only one phase. This feature provides operational flexibility and supports different grids in different regions.
- This phase configuration capability allows a single OBC design to be used universally—for instance, in regions like the USA, which primarily utilize single-phase grids, as well as in Europe, where three-phase grids are common.
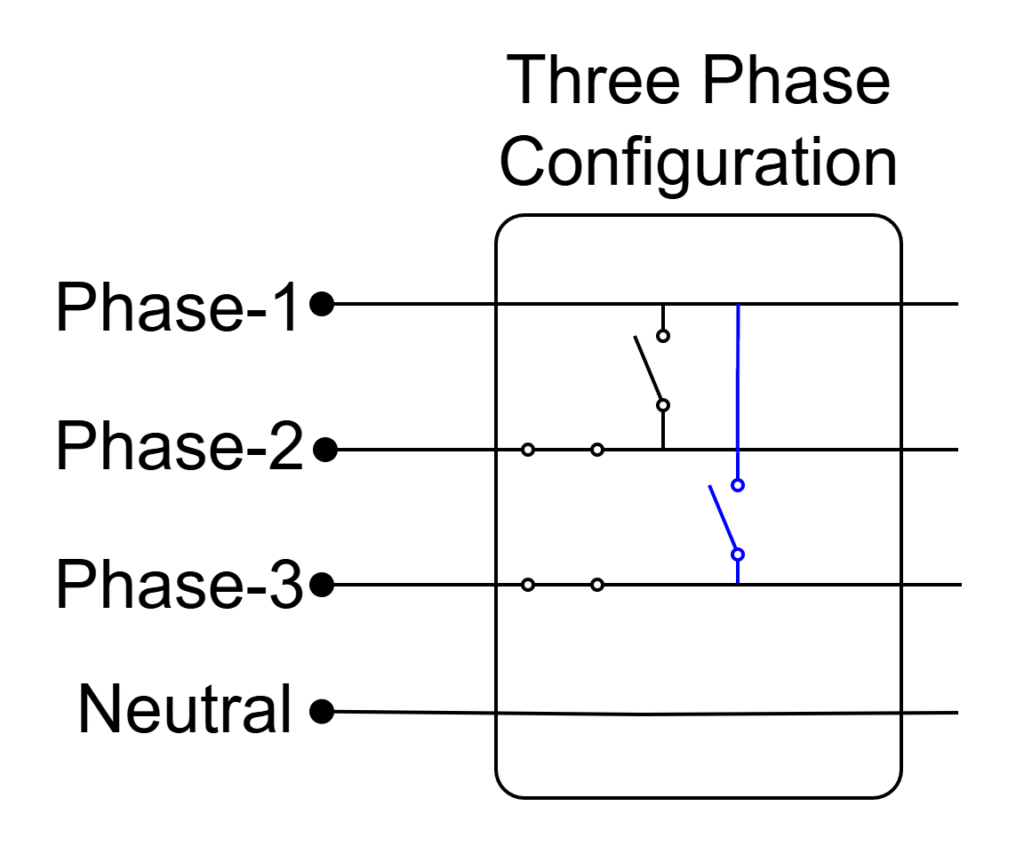
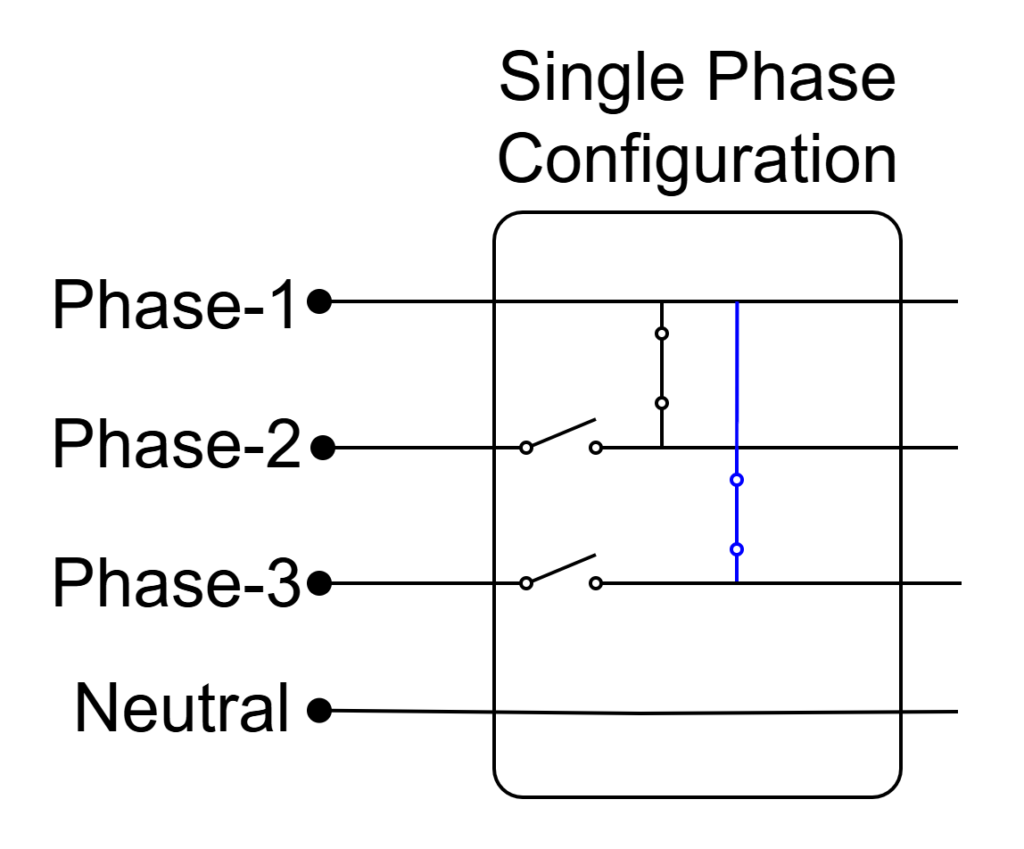
- EMI/EMC Filter:
- Filters out electromagnetic interference and ensures compliance with electromagnetic compatibility standards to prevent interference with other systems.
- AC to DC Conversion:
- Converts the incoming AC power from the grid into DC power, serving as the initial low-frequency conversion stage essential for subsequent processing.
- PFC Circuit:
- Power Factor Correction (PFC) is used to improve the efficiency of power conversion by ensuring that the input current is in phase with the input voltage. PFC helps to reduce the amount of wasted power and harmonics in the system. It corrects the power factor, typically aiming to achieve a value close to 1, meaning the power is used more effectively. This results in less strain on the electrical grid and ensures that the OBC operates with optimal performance.
- DC to AC Conversion:
- Converts DC power into high-frequency AC power. The reason for converting to high-frequency AC is that high-frequency AC allows for smaller, more efficient components like transformers, which are used in the next stage.
- High-Frequency Transformer:
- The high-frequency transformer is used to step up or step down the voltage while maintaining a high-frequency AC signal. The high-frequency nature of the transformer allows it to be much smaller and lighter than traditional low-frequency transformers, making it ideal for compact designs in an OBC. The transformer also provides electrical isolation between the input and output circuits, which is important for safety.
- AC to DC Conversion (in DC to DC conversion):
- Converts high-frequency AC back to DC after the transformer stage. This ensures the output power is suitable for the battery.
- DC Filter:
- Smoothens the output DC to ensure it is stable and free of ripples before being delivered to the battery. Clean DC power is critical for battery health and longevity.
- Main Controller:
- A microcontroller that manages all OBC operations, including power conversion, monitoring, communication, and safety protocols. It ensures that the OBC operates within predefined parameters and responds to system inputs dynamically.
- HVIL (High Voltage Interlock Loop):
- Monitors the integrity of high-voltage connections. Read more details about HVIL at HVIL Explained
- Sensors:
- Monitors various parameters, including:
- Input AC phase voltages, AC phase currents, and AC frequency.
- Output DC voltage and DC current.
- Temperature at critical points for thermal management.
- Monitors various parameters, including:
- Protection Mechanisms:
- Provides overvoltage and overcurrent protection at both the input and output.
- Includes thermal protection to prevent overheating.
- In the event of any faults, the OBC will immediately stops power conversion to ensure safety.
Major Functions of the OBC in EV:
The OBC performs several key functions to ensure reliable and efficient charging:
- Charging Modes:
- Constant Current (CC) Mode: Maintains a steady current during the initial charging phase, which is crucial for rapidly increasing battery charge.
- Constant Voltage (CV) Mode: Maintains a steady voltage as the battery nears full charge to prevent overcharging.
- OBC has to operate in above CC and CV modes as per the setpoint requested by the EVCC. This ensures that battery receives the optimal charge profile for its chemistry and state of charge. More details about these modes can be read at EV Charging Modes
- Fault Handling and Derating:
- Operates in a derating mode under fault conditions, such as high temperatures, to prevent OBC damage.
- Wide Operating Range:
- Supports input AC phase voltages from 80V to 270V (approx..) and frequencies from 45Hz to 65Hz (approx..), ensuring compatibility with various grids. This flexibility is essential for global applicability.
- The output DC operating voltage range depends on the battery voltage used in the EV. For typical 400V applications, the OBC is designed to support a voltage range from 300V to 500V (approx.).
- Communication:
- Exchanges key parameters with the EVCC, such as:
- AC phase voltages and currents.
- Frequency.
- DC voltage and current.
- HVIL status. Read more details about HVIL at HVIL Explained
- Communicates its power limits to assist the EV in planning charging requirements. For example, under normal operating conditions, the OBC reports its full power rating. In the event of overheating, it will report a reduced power limit.
- Exchanges key parameters with the EVCC, such as:
- Diagnostics:
- Logs fault information for maintenance and troubleshooting.
Challenges:
There are few challenges for OBCs in modern EVs which include:
- Size and Weight Constraints: One of the key challenges for OBCs in electric vehicles is minimizing size and weight without compromising performance. As EVs strive to optimize space and reduce weight for better efficiency and range, OBCs must be compact yet capable of handling high power conversion. Achieving this balance often involves using advanced materials and innovative designs, which can increase complexity and cost. Additionally, efficient heat dissipation becomes more difficult as the size and weight of the OBC decrease, making thermal management a critical aspect of OBC design.
- Bi-Directional Power Capability: With the rise of Vehicle-to-Grid (V2G) technology and the growing interest in bi-directional charging, integrating this feature into OBCs presents several challenges. Bi-directional OBCs allow power to flow both from the grid to the vehicle and vice versa, enabling vehicles to supply energy back to the grid or power external loads. However, supporting bi-directional power requires more advanced circuitry and control systems to manage the flow of electricity in both directions safely and efficiently. It also increases the complexity of the OBC’s design, as it must be able to switch between charging and discharging modes, and maintain compatibility with grid infrastructure.
The power rating of an OBC varies based on the vehicle type. While 7kW is commonly used, many modern EVs are equipped with OBCs rated at 11kW or even 22kW for faster charging capabilities.
The EVCC can be integrated into the OBC based on vehicle design needs. However, it is generally kept separate to support both AC and DC charging, maintain modularity and flexibility, and allow for the separation of functions (OBC for power conversion and EVCC for communication), optimizing each system for its specific role.
In conclusion, the OBC plays a crucial role in the EV ecosystem by converting AC power from the grid into the DC power needed to charge the vehicle’s battery. While OBCs are essential for efficient and safe charging, their design and operation present several challenges, including size and weight constraints, thermal management, voltage compatibility, and the integration of advanced features like bi-directional power capability. As the demand for faster charging and improved energy efficiency grows, addressing these challenges will be key to the continued advancement of OBC technology and the overall development of the electric vehicle industry.
EV Charging Explained – Everything you need to know about Electric Vehicle Charging